More than just logistics
Integrity of manufactured products hangs from a ‘digital thread’
News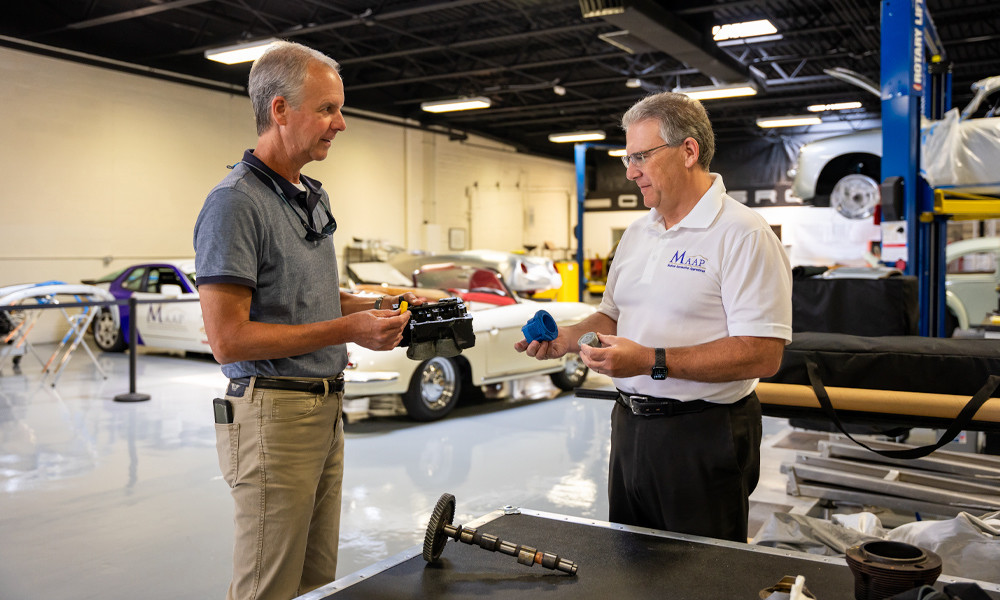
SUMMARY: Self-renewing supply chains of the future must come to terms with cybersecurity concerns.
When Bill Ritchie, CSX professor of Business Management in JMU’s College of Business, went looking for a partner to help him demonstrate to supply-chain students how 3D scanning and printing can provide a margin of safety against disruptions and downtime, he found one in a place some would find unlikely — the Carrier Library.
Ritchie says it was JMU Libraries employee Art Pekun who expertly scanned and rendered engine parts from his vintage Porsche 914, which was undergoing restoration in the laboratories of the Madison Automotive Apprentice Program. Pekun made careful notes as each part came off Ritchie’s engine, then took the parts back to the 3SPACE at the library for printing.
(3SPACE is the nation’s first 3D printing classroom at a general-education college. With the Carrier Library currently undergoing renovation and expansion, 3SPACE has temporarily been relocated to Lakeview.)
“Despite each part having been scanned and printed independently from the others,” Ritchie says, “the completed components fit together in the engine case and rotated smoothly.”
It was proof-in-principle of the power of “additive manufacturing” to extend the useful life of complex devices that may be subject to sabotage as well as the usual wear-and-tear. Additive manufacturing has become an important topic for supply-chain managers dealing with equipment failures in locations where it is difficult—if not impossible—to source and produce replacement parts, or when the manufacturers of the original equipment have long since halted production and gone out of business.
"What we're talking about," says Ritchie, "is a process of building up something from nothing,” using a composite material that mimics the medium from which the original component was fabricated.
Cole Scrogham (’90,’16M), founder and CEO of MAAP envisions a day when most automobile-parts departments will consist of nothing more than a 3D printer and a supply of raw material.
"Parts won't be kept on the shelf anymore," Scrogham predicts. "They'll just be printed out on-demand."
For Ritchie, the concept of a "digital thread" unique to each manufactured component holds the key to optimizing the process. What the U.S. Air Force is doing with its F-16 fighter jets, he and his “Introduction to Supply-Chain Management” (MGT461) students are also doing — but on a vastly different scale. However, the technologies and processes are the same, he says.
“Whatever it is, you can scan it, digitize it and then print out the actual component you need to replace,” says Ritchie.
The “elephant in the living room” is cybersecurity, he says.
Problems can arise, Ritchie explains, when someone in possession of a component part that exists only as lines of computer code in a file or on a chip then tries to transfer that component to someone else. It may be subject to interception or corruption by a competitor or rival application.
He characterizes cybersecurity for the digital thread as “uncharted territory” right now, but thinks it could represent “a real opportunity” for a university willing to move forward quickly.
In Ritchie’s view, effective cybersecurity for the digital thread will remain out of reach without the cross-functional partnerships that naturally occur in a university setting.
“I think JMU is uniquely positioned for these types of collaborative efforts," he says.