Exploratory Study on the Current Limitations of Personal Protective Equipment and the Potential for Innovation
CISR JournalThis article is brought to you by the Center for International Stabilization and Recovery (CISR) from issue 25.2 of The Journal of Conventional Weapons Destruction available on the JMU Scholarly Commons and Issuu.com.
By Kyaw Lin Htut [ Norwegian People's Aid ]
All images courtesy of Norwegian People’s Aid.
Personal protective equipment (PPE) in mine action typically consists of a polycarbonate visor that fully covers the face and front neck, and body armor consisting of an apron made of aramid fabric (i.e., Kevlar) that fully covers the front torso, groin, and neck. PPE used in mine action is generally considered as “the last line of defense” since the primary method through which accidental deaths and injuries are prevented is through the application of and adherence to appropriate standard operating procedures (SOPs). However, with any operations, there is always an element of “acceptable risk,” and universal adherence to all SOPs at all times by all mine action personnel is not realistic. Thus, the primary purpose of PPE is to minimize harm rather than prevent it. This must be balanced with factors such as weight, mobility, visibility, and to a lesser extent, cost.
In volume 22, issue 1 of this publication, Andy Smith observed that there has been a lack of progress in PPE development for the last twenty years. He attributes this to a combination of factors including
- “Lack of demand.”
- “The current risk is thought tolerable.”
- “More immediate ways to manage risk.”1
Smith further notes that this trend has not been ideal, and that improvements to PPE technologies and usage should address four needs, namely
- “reduce the severity of blast injuries…[by adopting]…blast resistant hand-tools”
- “reduce eye loss…[through]…invention of improved visor material”
- “increase body protection”
- “allow end-users to compare products”
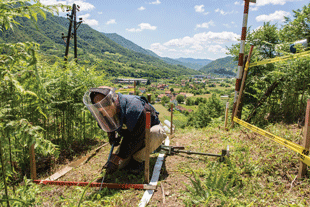
Male NPA deminer in Bosnia and Herzegovina conducting clearance while wearing aramid body armor and a polycarbonate visor.
Furthermore, the current generation of PPE used in mine action is geared towards threats that were more common in previous years (i.e., anti-personnel [AP] blast mines). As conflicts, threats, and mine action activities evolve, for instance with the increasing use of IEDs and greater emphasis on cluster munitions and other unexploded ordnance (UXO) clearance (particularly in populated areas), there needs to be periodic review to ensure that the current generation of PPE is “fit for purpose.” As mine action activities have progressed beyond the clearance of primarily AP mines, the need for a new generation of PPE becomes apparent as evolving threats, environmental impact, and gender inclusivity should be taken into account.
Hoping to further clarify and fulfill these needs in 2021, Norwegian People’s Aid (NPA) received a grant from Innovation Norway to investigate the criteria for and facilitate the development of the “Next generation of Personal Protective Equipment (PPE) in Mine Action and Disarmament.” To that end, this paper expounds upon Smith’s analysis, further identifying and considering some of the major limitations in the current generation of PPE typically used in the mine action sector. This paper explores the technical limitations of the materials used as well the operational constraints and in doing so, develops a framework through which next generation PPE suited to mine action operations can be developed.
High-Velocity Fragmentation Threats
High-velocity fragmentation2 presents a unique challenge in humanitarian mine action (HMA)3 due to the fact that most PPE used in HMA is typically not rated to defeat this threat. According to International Mine Action Standards (IMAS) 10.304 the minimum standard of body armor must be at least NATO Standardization Agreement (STANAG) 2920 compliant to V50450 at 1.102 g, meaning that the material must reliably stop 50 percent of incoming projectiles with a mass of up to 1.102 g travelling at 450 m/s. IMAS 10.30 does not specify that visors need to be STANAG 2920 rated, only that “the eye protection shall be capable of retaining integrity against the blast effects of 240 g of TNT at 60 cm and shall provide protection equivalent to not less than 5 mm of untreated polycarbonate” (IMAS 10.30, 2013).5 With this in mind, however, it must be noted that the PPE used in HMA is primarily intended to mitigate the effects of secondary fragmentation6 from AP blast mines rather than high-velocity fragmentation. Although the technology to defeat high-velocity (i.e., rifle) projectiles widely exists in the form of ceramic-composite or high-hardness steel, the significant added weight, loss of flexibility, and bulk (some plates are as thick as 25 mm) for a limited coverage area and high cost of procurement are significant drawbacks to widespread adoption.
Although large caliber ordnance such as artillery shells produce high-velocity fragmentation,7 this paper will only refer to smaller AP items such as cluster munitions, grenades, and AP fragmentation mines encountered during HMA operations. The reason for excluding larger caliber items is that the probability of survival of a point blank (i.e., within 1 m) detonation of a large caliber projectile (with more than 1 kg of high explosive) is virtually zero, while survival of a point blank detonation of smaller items such as AP fragmentation mines, grenades, or cluster munitions have been extensively documented by NPA and the mine action sector as a whole.
Using this criteria, there have been in total fourteen high-velocity fragmentation accidents involving cluster munitions, AP fragmentation mines, and grenades resulting in sixteen casualties documented in NPA’s database from January 1994 to April 2020. These accidents have resulted in the deaths of eight victims and non-fatal injuries to eight survivors. Of the eight fatalities, five8 were not wearing any torso PPE (i.e., body armor) or facial PPE (i.e., visor) and all five received fatal penetrative injuries to the torso as well as fatal head injuries from high-velocity fragmentation. Of the three fatalities who were wearing body armor, two of the victims had parts of their body armor compromised, while one did not have their body armor compromised and received no torso injuries (the victim received penetrative head injuries). Of the two fatalities with compromised body armor, one received undocumented non-life-threatening injuries to the torso and one received life-threatening injuries to the torso. All three fatalities were wearing a polycarbonate visor, which had been compromised causing fatal head/facial injuries to the victim.
Of the eight survivors of accidents involving high-velocity fragmentation over the same period, seven were wearing both body armor and visors. The remaining individual who was not wearing any PPE had survived due to their location behind another (unprotected) victim who did not survive.9 Of the seven survivors wearing body armor, two had their vests compromised and suffered penetrative torso injuries. Two of those who did not have their body armor compromised still received penetrative torso wounds due to side impact in areas not covered by their PPE, but survived these injuries. The visors worn by seven survivors were not compromised, although three received superficial facial injuries and one survivor lost an eye due to blast overpressure and debris entering their visor.
While sixteen individuals is too small of a sample size to establish any statistical or causal relationship, the anecdotal information from NPA’s records indicate that ten of the sixteen individuals involved in high-velocity fragmentation accidents were wearing PPE, seven of whom survived with varying degrees of injuries (70 percent survival). Body armor was compromised in four out of these ten cases (40 percent) with victims receiving injuries to the torso, with two out of the four victims surviving those injuries (50 percent survived despite their body armor being compromised). Visors were compromised in three out of the ten cases (30 percent) with victims receiving injuries to the head or face; none of the victims survived these injuries. By contrast, of the six victims who were not wearing PPE, only one survived (16 percent survival).
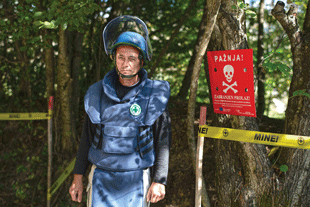
Male NPA deminer in Bosnia and Herzegovina wearing aramid body armor and a ballistic helmet with a polycarbonate visor.
While the information provided from these accidents does not take into account the method of injury and circumstances that could be aggravating or mitigating factors (i.e., victim position, fragmentation mass/density, velocity, angles, quality of casualty evacuation (CASEVAC), etc.) or the severity of injuries and lasting disabilities, it anecdotally illustrates that personnel wearing PPE do have higher survival rates in accidents involving high-velocity fragmentation, even if the PPE is compromised. However, personnel who have compromised visors from high-velocity fragmentation had significantly lower survival rates. This could hypothetically be attributed to a combination of the following factors:
Injuries to the head are much more catastrophic due to the vulnerability of the brain, and it being a much larger proportion of the “target area” (i.e., frontal profile of the face/head), as opposed to the torso where the chances of hitting a vital organ are proportionately lower.
The material properties of polycarbonate offer less protection compared to aramid (Kevlar) by volume and weight.
The mechanism of failure of polycarbonate visors could potentially be a “shattering” effect, which also enables more kinetic energy to pass through into the victim causing more catastrophic injury. By comparison, it could be argued that aramid fabric is able to absorb and redistribute kinetic energy more efficiently than polycarbonate.
Both polycarbonate and aramids are subject to degradation due to environmental factors such as UV light, moisture, and general wear and tear. This would begin to degrade the protective performance of these materials over time. It could be argued that polycarbonate could deteriorate at a faster rate due to increased exposure to the elements when compared to aramid fabric (which is usually contained within a water-resistant pouch).
Taking these factors into consideration, it must also be noted that the relationship between the kinetic energy of a projectile and the severity of injuries (e.g., traumatic bone and soft tissue damage) has been extensively documented in medical journals and other publications. According to Rozen and Dudkiewicz’s chapter “Wound Ballistics and Tissue Damage” in Armed Conflict Injuries to the Extremities: A Treatment Manual:10
The amount of tissue damage and the injury severity of gunshot injuries are due to the energy transmitted by the bullets or projectiles, depending mainly on their velocity. Therefore, the injuries are not divided any more, as in the past, to ‘high- and low-velocity injury’ but to ‘a high- or low-energy injury.
This understanding is further supported by Hauer et al.:
Although a large number of factors influence the missile in flight and after penetration of the body, the most important factor is the amount of energy transmitted to the tissue. Shrapnel wounds are usually produced with similarly high kinetic energy to those caused by hand- and long guns. However, fragments tend to dissipate the entire amount of energy within the body, which increases the degree of tissue disruption.11
One of the main mechanisms through which tissue damage is achieved is through cavitation, in which a high-energy projectile will cause large wound cavities as a result of energy transfer. This is further exacerbated by internal lacerations, tumbling, and fragmentation of the projectile within the victim, as well as secondary fragmentation of bone causing additional injury. According to Rozen and Dudkiewicz, these factors are “thought to be the most significant factor in tissue injury from high energy projectiles.”12
Rudimentary Theoretical Model of Fragmentation Impact Energy on PPE
The mechanics through which PPE is compromised may be a combination of factors including impact kinetic energy (a function of velocity and mass), cross-sectional density, and hardness of the projectile as well as impact and deflection angles. In order to develop a simplified theoretical model to study the effects of fragmentation, this paper will limit these to two factors, namely the kinetic energy of the incoming projectile and the kinetic energy impact resistance rating of the typical PPE material. One can therefore develop a hypothesis that if the kinetic energy of the impact exceeds the resistance rating of the PPE material, then the probability of penetration of the PPE material will be higher.13 For further simplification, this model will assume that there is no further fragmentation of the projectile upon impact and the hypothetical kinetic energy passed through to the victim would be the residual kinetic energy after the impact (kinetic energy of the impact minus the resistance rating), thereby representing an analogue for potential severity of injury.
IMAS 10.30 lists a minimum requirement for torso protection to be STANAG V50450 at 1.102 g, which equates to 111.78 J of impact kinetic energy (kinetic energy = 1/2 m v2.14 As such, torso protection in the HMA sector is typically comprised of aramid fabrics (Kevlar) providing soft armor to STANAG 2920 V50450 fragmentation protection. This standard is defined as body armor stopping a series of projectiles being launched at 450 m/s at least 50 percent of the time.15 Bolduc and Jager further define fragmentation types and mass, with R7 being the highest mass “right angled, circular cross-section (RCC)” projectile.” Therefore, if a soft (aramid) body armor type is rated V50450 R7, then it is rated to stop 50 percent of unsaboted, RCC projectiles with a maximum mass of 4.15 g travelling at 450 m/s, and the theoretical impact kinetic energy (in joules) of this projectile would be 420.185 J. By comparison, the most common form of facial protection in compliance with IMAS 10.30 are polycarbonate full face visors that are at least 5 mm thick. According to the technical manual of one polycarbonate manufacturer, SABIC, their 5 mm polycarbonate sheets are rated up to 370 J of impact.16
In order to compare the differences in kinetic energy impact of a typical piece of primary fragmentation versus secondary fragmentation, the following formulas will be used as the basis for calculating the velocity (V) upon impact of the respective projectiles.
The starting velocity of primary fragmentation from a metal bodied ordnance is determined by the respective Gurney equation17 (see Figure 1), which takes into account the body shape of the item (spherical or cylindrical) and the velocity of detonation of the explosive charge (dependent on explosive type).
Cylindrical Charge Equation |
V = initial fragment velocity (m/s) √2E = Gurney Constant for a given explosive (m/s) M = mass of fragment (kg) Cexp = explosive charge mass (kg) |
Spherical Charge Equation |
|
Figure 1. Gurney equations for cylindrical and spherical bodies. |
The initial velocity calculated from a respective Gurney equation for cylindrical or spherical bodies can then be used to further calculate the estimated velocity of a piece of fragmentation (and thus also the energy) at a determined range as a function of air density, cross-sectional area, drag, and fragment mass.18 This is shown in Figure 2.
V(s) = V0 * e-(p*Cd*A*S)/(2*m) |
V(s) = velocity at desired distance V0 = velocity of the fragment at the point p = atmospheric density (kg) = 1.2 kg/m3 at sea level. Cd = drag coefficient (dependent on fragment shape) For reference, a perfect smooth sphere has a Cd of 0.47 at subsonic speeds and around 1.1 at supersonic speeds while a flat plate has a Cd of 1.28 (NASA, 1993).19 The US Department of Defense Explosives Safety Board recommends using a Cd of 1.28 as an average to model fragmentation drag of any given item (Department of Defense, 1975).20 A = cross sectional area of projectile (in square meters) S = desired distance in meters M = mass of projectile (in kg) |
Figure 2. Function of fragment velocity over distance travelled. Figure courtesy of Federation of American Scientists. |
Separately, according to the U.S. Department of Defense (DoD), the estimated approximate maximum range for secondary fragmentation is shown in Figures 3 and 4.
Rocks 29.2 / NEQ0.4 |
Soil 12.5 / NEQ0.4 |
Figure 3. Theoretical maximum range of projectile material type per scale of NEQ. Figure courtesy of U.S. Department of Defense, 1975.21 |
Furthermore, simple estimates of theoretical maximum range of fragmentation (primary and secondary) can be calculated using the following function:
R = (V0 / g) * Sin 2θ |
R = Range (m) V0 = Initial Fragment Velocity (m/s) g = Gravity (m/s2) (Earth gravity constant is 9.82 m/s) θ = Launch Angle (Radians) |
Figure 4. Function of fragmentation maximum theoretical range. Figure courtesy of IATG, 2015. |
Using these functions, the following are illustrative examples of fragmentation velocity and impact kinetic energy calculated for comparisons between primary fragmentation from a BLU-26 submunition and secondary fragmentation from a PMN AP blast mine.
A BLU-26 cluster bomb has a body mass of 0.350 kg, a net explosive quantity (NEQ) of 0.085 kg of Cyclotol, and an All Up Weight (AUW)22 of 0.435 kg. It is generally spherical in shape and holds 600 small steel balls of fragmentation embedded within the metallic body. It has a diameter of 0.064 m (64 mm) and a radius of 0.032 m.23 Using these dimensions, the spherical surface area of the item is 0.0128 m2 (or 12,867 mm2), and using these specifications, it is possible to calculate the initial velocity of the metal fragments at the point of detention with the spherical Gurney equation for Cyclotol as follows:
V = (((M / Cexp) + 3/5))-1/2) / √2E
V = (((0.35 / 0.085 + 0.6))-1/2) / 2,402
V = 1,106 m/s
Although there are 600 tiny ball bearings contained within the body, these balls are embedded in the metal itself. Therefore, we will assume that these bits will fragment chaotically (some still attached to the metal casting while others will be ejected cleanly). With this in mind, we can assume that 300 spheroid pieces of fragmentation are released on average from the body, with an average mass of 0.0011 kg (1.1 g). The average cross-sectional surface area of each fragment will be assumed to be the overall spherical surface area divided by 300, which gives us 0.00004 m2. Therefore, assuming that the item detonates 1 m away from the victim, it is possible to calculate the estimated average velocity of each fragment at 1 m away from the point of detonation (at sea level) using the formula provided by the Federation of American Scientists shown here:
V(s) = V0 * e-(p*Cd*A*S)/(2*m)
V(1) = 1,106 * e-(1.2*1.28*0.00004*1)/(2*0.0011)
V(1) = 1,072.5 m/s
Thus, at 1 m from the point of detonation, the pieces of fragmentation will have an estimated velocity on average of 1,072 m/s at sea level. Assuming that each projectile has a mass of 1.1 g, then the kinetic energy upon impact can be estimated to be around 575 J (0.5 * 0.0011 * 1072.52). The velocity and energy at every meter of distance travelled can also be calculated and is shown in Figure 5.
Using this basic fragmentation model as the underlying assumption, it is estimated that during a BLU-26 accident at 1 m, a 1.1 g fragment will impact with 575 J of kinetic energy. Assuming that 5 mm of polycarbonate is resistant against 370 J under perfect theoretical conditions of impact, at least 205 J of energy will still be retained by the fragment once a polycarbonate visor is comprised. Likewise, assuming that STANAG V50450 R7 vest can resist up to 420 J under perfect theoretical conditions, the kinetic energy that is retained by the fragment after a body armor vest has been compromised would be at least 155 J under perfect conditions. Without PPE, the victim would theoretically suffer the impact of the entire 575 J of kinetic energy from a single fragment.
By comparison, one can also model the velocity of a 1 cm3 piece of rock that has been ejected from a PMN blast with the following assumptions:
A PMN mine has 240 g NEQ of TNT.
During the explosion, the entire PMN body is consumed, and therefore the pieces of plastic/Bakelite primary fragmentation will be excluded.
According to Encyclopedia Britannica,24 the average density of rock is 2.73 g per cm3. For simplicity´s sake, we will assume that the volume of this rock is precisely 1 cm3 (or 0.000001 m3) and is spheroid in shape.
The rock is launched at a 45-degree angle from the blast site. A 45-degree launch angle achieves the maximum theoretical range of any launched projectile.
Therefore, with an explosive weight of 0.24 kg of TNT in a PMN, the maximum theoretical distance that a rock is ejected from a blast is (as per U.S. DOD 1975 formula):
= 29.2 / NEQ0.4
= 29.2 / 0.240.4
= 51.67 m
Using the IATG simple fragment range estimation formula, it is possible to estimate the initial fragment velocity from a launch angle of 45 degrees (0.785 radian).
If:
51.67 = (V0 / g) * Sin 2θ
51.67 = (V0 / 9.82) * Sin (2 * 0.785)
Then:
V0 = 51.67 * 9.82 / Sin (2*0.785)
V0 = 507.47 m/s
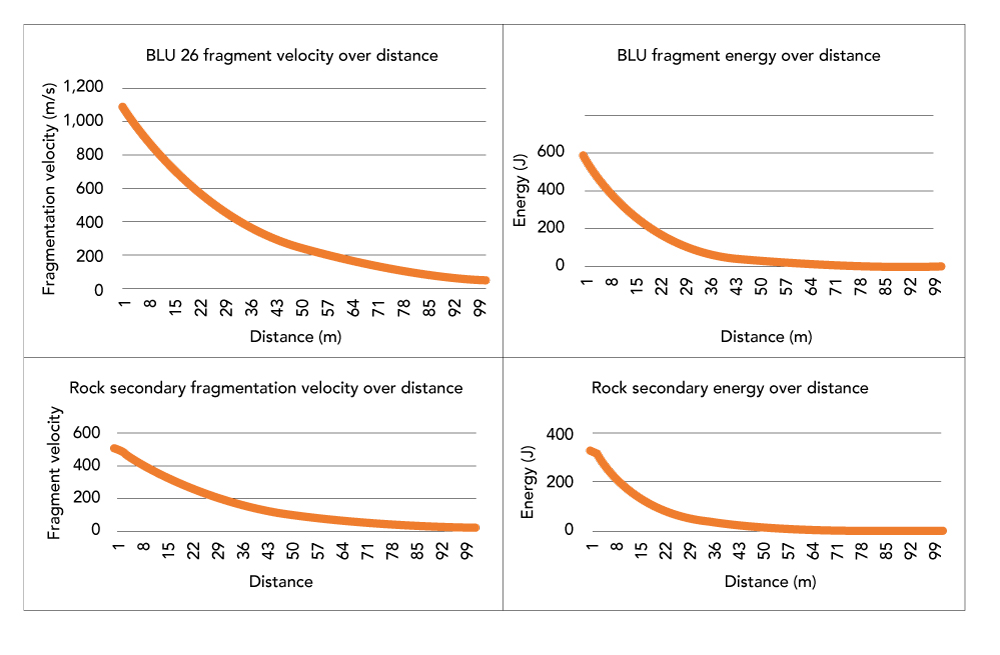
Figure 5. Graphs on the fragmentation emergency and velocity over distance. Figure courtesy of the author.
Now that we have the initial velocity of the rock (calculated from theoretical maximum range), we can calculate the travelling velocity at a given range. Given the assumption that the rock’s dimensions are a spheroid with a volume of 0.000001 m3, the radius (r) of the spheroid rock is roughly 0.006203 m (using r = (3 * V / 4π)⅓, calculated as 0.6203 * 0.0000011/3), and correspondingly its cross-sectional area, which will be the same as its circular area is 0.00012 m2 (calculated as π*0.0062032). Using this cross-sectional area, we can estimate the secondary fragmentation velocity at 0.6 m (as stipulated in IMAS) employing the Federation of American Scientists’ equation as follows:
V(s) = V0 * e-(p*Cd*A*S)/(2*m)
V(0.6) = 507.47 * e-(1.2*1.28*0.00012*1)/(2*0.0027)
V(0.6) = 497 m/s
Therefore, it is estimated that the rock will be travelling at a velocity of 497 m/s once it reaches 0.6 m (less than half the estimated velocity of the BLU-26 fragment at 1 m). Using the 497 m/s velocity at 0.6 m and the given mass of the rock being 2.7 g, the estimated impact energy of the rock is calculated at 333.6 J (i.e., 0.5 * (0.0027 * 4972)). This is within the 370 J impact rating of the 5 mm polycarbonate produced by SABIC and STANAG 2920 V50450 R7 limits for impact energy of 420 J.
Figure 5 illustrates the velocity and impact energies of BLU-26 primary fragmentation and secondary fragmentation from a PMN blast. In addition to PPE playing a significant factor in mitigating the transfer of kinetic energy, the standoff distance plays a significant factor as well. Projectiles rapidly decelerate, thereby also losing impact kinetic energy in the process.
Material Degradation of PPE and Environmental Impact of Disposal
Taking these scenarios into consideration, one can argue that the condition of the PPE can potentially affect its tensile strength, thereby decreasing its ability to absorb kinetic energy and enabling a higher probability of penetration by both primary and secondary fragmentation. The decreased level of protection offered by the degraded material would in turn permit more kinetic energy to pass through to the wearer. The degradation of both polycarbonate and Kevlar due to use and environmental factors has been extensively documented.
In the case of polycarbonate, exposure to ultraviolet (UV) light has been one of the main causes of material degradation.25 Significant yellowing occurs to the material and the polycarbonate loses its strength and elasticity. The mechanical properties of polycarbonate also change, becoming more brittle and crystalline. Under laboratory conditions, untreated polycarbonate begins to yellow within seventy-two hours of UV exposure and significantly yellows by 503 hours of UV exposure.26 Assuming that a polycarbonate visor is exposed to sunlight eight hours a day in field conditions, this would be the equivalent of 62.88 work days. Tensile strength decreases by 9 percent within 216 hours of UV exposure. This degradation means that polycarbonate visors lose their protective properties after continuous operational use, thereby gradually losing their ability to offer the level of protection specified in IMAS 10.30.
During regular operational/field usage, visors also accumulate scratches and other wear and tear, thereby further compromising the structural integrity. Additionally, the combination of scratches and yellowing of visors further adds to the diminishing of visibility for the user. IMAS Technical Note 10.10/0227 states that
Users should be aware that the polycarbonate material from which blast-visors are made is adversely affected by prolonged exposure to sunlight (UV light). The effect of sunlight isto create hardened areas from which a crack may propagate.
It further goes on to report instances where visors have shattered as a result of AP mine blasts, exacerbating the injuries received by victims. Even in cases where polycarbonate is only used in a relatively limited capacity such as in ROFI’s demining mask (the mask is primarily made from laminated composite materials with a polycarbonate vision slot), the use of polycarbonate presents a potential “single point failure” scenario.
A test of a new mask in 2008 by the Swedish Rescue Services Agency conducted on 240 g of TNT equivalent placed on the surface on sand with a 70-degree blast angle at 55 cm showed that the polycarbonate vision slot of the mask shattered while the rest of the mask was not compromised during the blast.28 A similar test done on 140 g of TNT equivalent showed both the polycarbonate vision slot and the composite components of the mask withstanding the blast. According to ROFI, an internal test with the blast of a PMA-1A (presumably containing the standard 200 g of TNT) at 55 cm showed that the mask withstood the blast without being compromised (ROFI).29
Aramid fabrics such as Kevlar used in body armor also suffer from degradation due to continual use. In particular, degradation as a result of long-term exposure to moisture and mechanical ablation from friction has been documented. According to Forster et al., p-phenylene terephthalamides (PPTA) body armor such as Kevlar and Twaron had a theoretical 10–13 percent decrease in V50 rating resistance after artificial aging simulating the temperature, humidity, and mechanical wear of typical field use over five years.30 Likewise, Grant et al. reported a 10 percent reduction in V50 ballistic performance of five-year-old, United States National Institute of Justice (NIJ) Level IIIA and Level II body armor taken from a random sample of field users.31 Direct exposure of aramids such as Kevlar and Twaron to the natural elements conducted in hot and humid environments have reported up to an 80 percent decrease in tensile strength.32 Possible explanations for this include water and other liquid ingress causing the “slippage of yarns of aramid fabric in wet conditions,”33 as well as mechanical wearing of the fibers caused by repeated folding and rolling34 simulating conditions worn in the field.
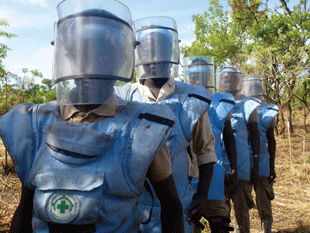
NPA deminers in South Sudan wearing aramid body armor and polycarbonate visors.
As a result of degradation, body armor manufacturers typically provide a five-year warranty and it is recommended that users replace the body armor every five years of regular use or the period recommended by the manufacturer.35 IMAS Technical Note 10.10/02 also recommends that “visors manufactured from untreated polycarbonate are replaced annually or every 225 days of use in order to minimise risks of degraded protection as a result of UV exposure.”36 Taking this into consideration, environmentally-sound methods of disposal employed by HMA operators may not typically be available in countries that they work in.
Kevlar in its final form is very hard to destroy and will not naturally decompose in a landfill. Although there exists various energy and capital-intensive recycling methods such as chemical and thermal breakdown (pyrolysis) of the materials, it is not yet at a stage to be economically viable.37 Relatively new methods such as thermal degradation, as proposed by Dabkiewicz et al., have yet to be fully commercialized.38 Although there are various companies that specialize in the recycling of Kevlar, these companies are not present in many developing countries where mine action operators normally work. Shipping unserviceable Kevlar internationally will also likely not be cost-effective, particularly for humanitarian organizations.
As stated previously, visors have a relatively short service life and polycarbonate material is not as easily recyclable as other plastics such as polyethylene. Polycarbonate is typically recycled through thermal and chemical processes that break down and reconstitute the material. As it is for recycling Kevlar, the processes for recycling polycarbonate are not readily available in most of the countries where HMA is being conducted due to its technical and capital-intensive nature. As a plastic polymer, polycarbonate does not naturally bio-degrade in landfills and particulate shedding can occur which can further add to microplastic pollution. For example, Zhang et al.,39 estimate that 310 t of microplastic polycarbonate enter water systems annually in the form of sewage sludge in the United States. Polycarbonate waste has been documented to leach a precursor additive compound bisphenol A (BPA) into water sources. Although longitudinal public health implications have yet to be studied, evidence presented by Konieczna et al.,40 suggests a strong relationship between prolonged BPA exposure and endocrine disorders in humans. According to Morin et al.,41 “BPA is commonly found in landfill leachate at levels exceeding acute toxicity benchmarks” and in Norway it was reported that concentrations of 188 mg +-125 mg of BPA leachate was present in every 1 kg of solid plastic waste.42 To the author’s knowledge, there have not yet been any definitive studies on the proportion of polycarbonate in overall global plastic waste and the extent to which this has caused environmental damage in developing countries (particularly mine and explosive remnants of war [ERW]-affected countries) is unreported.
Taking all of this into consideration, HMA operators can potentially release several tonnes of polycarbonate and aramid waste every few years due to the need for replacement of visors and body armor. If for example a mine action operator deploys 1,000 deminers wearing full face polycarbonate visors and body armor in a country program, then the operator may be expected to discard up to 1,000 visors every year if it complies to IMAS 10.10/02 recommendations and up to 1,000 kits of body armor every five years. With a typical standard full-face visor from a manufacturer such as Security Devices weighing around 1 kg and body armor (i.e., Apron) weighing between 2.5 and 3.9 kg,43 this would equate to 1 t of polycarbonate waste produced every year and 2.5–3.9 t of aramid waste produced every five years by that operator’s country program alone.
For perspective, NPA employs 1,441 mine action operational staff globally as of September 2021. From anecdotal reports, mine action operators typically put unserviceable PPE into long-term storage, however it is not immediately clear what will happen thereafter and what the end-of-life cycle process of this waste disposal will be. If for instance the items are discarded in local landfills, the environmental concerns as highlighted previously may be particularly acute. Likewise, if the items are incinerated, there will likely be significant carbon emissions and particulate air pollution. There are also ethical concerns regarding the practice of international operators donating unserviceable or expired PPE to national operators and national authorities, particularly if the materials have degraded to such an extent as to offer decreased protection below national standards and/or IMAS 10.30. It can also be the case that operators may not know when and why PPE needs to be replaced, thereby continuing the use of degraded or unserviceable PPE in the field and adding unnecessary risks.
Gendered Perspectives on Comfort and Ergonomics
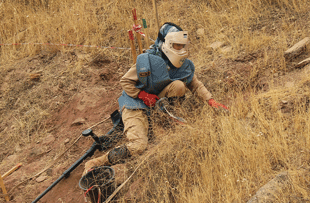
Female NPA deminer in Tajikistan conducting clearance in difficult terrain while wearing aramid body armor and a demining mask.
While the technical drawbacks and limitations in the appropriateness, use, and disposal of PPE have been explored throughout this paper, it is also important to factor in the comfort level of PPE for the wearer, to further enable a safer and more productive work environment. As stated previously, although there are commercially available products that can provide increased protection, this comes at a significant penalty in weight, bulk, and discomfort for the wearer (not considering cost). Although there have been technological developments in body armor such as the increased use of ultra-high molecular weight polyethylene (UHMWPE) and innovative facial protection systems that use composite materials combined with reduced use of polycarbonate such as ROFI’s demining masks, widespread adoption has been relatively limited.
Furthermore, just as threats and protective technologies change over time, so too has the face of mine action. Whereas in the past, mine action operations (particularly demining and EOD) have been almost exclusively conducted by men, there is now greater participation of women both as operational staff and as leaders. According to IMAS 10.30, “PPE provided shall fit the employee, male or female, and be designed to provide reasonable comfort and protection against the predictable risks present at a demining worksite. Cultural practices should also be taken into consideration.”44 Unfortunately, almost all PPE used in the HMA sector is unisex and not optimized toward female wearers. This causes discomfort and potentially reduces the safety of the equipment and the wearer’s operational efficiency. Although female-specific body armor is now commonly used in the law enforcement sector around the world, these developments have not yet been adopted within the mine action sector. Unisex body armors are typically designed according to the size, body shape, and/or proportions of men; however, when issued to women, the only difference is that they are issued in smaller sizes.
For this reason, the author hypothesizes that the current generation of PPE may not provide the full coverage, comfort, or functionality for women when compared to men. One of the first activities encompassed in the Innovation Norway grant is to develop and field next generation PPE. With this in mind, NPA conducted an internal global survey of 340 participants working in field operations; 65.6 percent of whom were women. In total, 83.8 percent of respondents worked as a deminer or team leader. Highlights from the preliminary results showed that:
- 13.53 percent of respondents reported their body armor as being overall uncomfortable or very uncomfortable
- 25 percent of respondents reported some form of abdominal pain or discomfort while wearing body armor
- 25.89 percent of respondents reported reported their visors as being overall uncomfortable or very uncomfortable
- 25.89 percent of respondents reported some form of hip pain or discomfort while wearing body armor
- 26.47 percent of respondents reported some form of genital/groin pain or discomfort while wearing body armor
- 27.36 percent of respondents reported some form of inner thigh pain or discomfort while wearing body armor
- 27.65 percent of respondents reported some form of breast pain or discomfort while wearing body armor
- 34.11 percent of respondents reported some form of lower back pain or discomfort while wearing body armor
- 39.70 percent of respondents reported some form of difficulty breathing while wearing visors
- 41.76 percent of respondents reported some form of shoulder pain or discomfort while wearing body armor
- 48.23 percent of respondents had some form of head or neck pain while wearing visors
These preliminary results appear to be consistent with the initial assumption that improvements in ergonomics are necessary, particularly as it relates to women. In addition to the various cultural taboos in developing and post-conflict countries for women in what was traditionally seen as male-dominated work, the lack of ergonomic optimization of PPE for women may also be a factor in creating further barriers to female participation in the mine action sector.
Conclusion and Prospective Innovations
Through analysis of casualties from high-velocity fragmentation, analyzing the kinetic energy impact of fragmentation, and conducting a literature review on the degradation of polycarbonate and aramids, the existing evidence appears to suggest that any new developments in PPE should minimize or completely forego the use of polycarbonate for visors, and at the very least pursue ways to better seal aramid materials against the elements. This would enable more consistent levels of IMAS 10.30 compliant V50450 protection of both body armor and visors. Further exploration is also needed on finding ways to improve protection beyond the level stipulated in IMAS 10.30, particularly against high-velocity fragmentation, without increasing weight and bulk or reducing visibility. Careful consideration will also be needed to ensure the environmentally sustainable disposal of expired or unserviceable PPE and/or ways to prolong the service life of existing serviceable stocks. As of this writing, NPA is conducting further studies to determine the life-cycle management of PPE in its country programs. Underlying all of this is the cross-cutting theme that any development and advancement in PPE must be gender-sensitive and take into account user feedback on comfort, mobility, and visibility, particularly from female users. It must also be noted, as argued by Smith, that cost will always be a factor in enabling widespread adoption, therefore any new solutions proposed must be cost-effective and on par with the cost of replenishing current generation PPE.
In support of these conclusions, NPA will be pursuing the following lines of inquiry:
Explore the incorporation of composite materials and new designs of visors that minimize the use of polycarbonate. Transparent materials in lieu of polycarbonate, treatments of polycarbonate, or a combination thereof will be also explored. One of the possibilities is to further optimize the demining mask design (or similar designs) to enable better visibility, breathability, and protection at a cost on par with untreated polycarbonate visors.
Explore portable low-cost solutions that can enable the safe destruction or recycling of unserviceable polycarbonate and aramids with the least environmental impact. These solutions must be implementable in austere environments.
Explore the use of ballistic fabrics that are more environmentally and mechanically resistant to wear and tear than aramid, develop better protective shells for current aramid PPE in service, and/or explore composite designs that offer the same levels of mobility and flexibility of aramid.
Conduct focus groups on how to best optimize and modularize PPE designs so that they can be more adaptable to female users.
NPA will subsequently be having a market dialogue wherein an open invitation will be announced for all companies and organizations interested in partnering with NPA under this Innovation Norway project in order to find potential solutions and jointly develop and field test scalable prototypes. ◊
Kyaw Lin Htut
Advisor/Desk Officer
Mine Action and Disarmament
Norwegian People’s Aid
Kyaw Lin Htut is a Desk Officer for Norwegian People’s Aid, Department of Mine Action and Disarmament. He previously served in various mine action operational and management roles in Southeast Asia and the Caucasus. As Desk Officer, he oversees a portfolio of country programs in Southeast Asia and the Pacific and also manages NPA’s projects with Innovation Norway. He is IMAS EOD Level 3 qualified and holds a master’s degree in economics.